Elco Electrocoagulation Contaminant Removal System Request a Quote
Electrocoagulation Technology
The electrocoagulation process is very similar to normal chemical coagulation – the difference is that it uses electrical energy. Both processes aim to destabilize the colloids contained in a quantity of water, but they differ in the method used to add the reagent: in conventional coagulation, the reagent is added as a salt, whereas in electrocoagulation, it is generated from a metal. Electrocoagulation can be defined as an electrochemical process during which the colloidal matter present in a quantity of wastewater is gathered together using compounds resulting from the dissolving of an anode in order to allow the colloids to be separated from the wastewater using conventional techniques. Because they dissolve, the anodes disappear during the course of the treatment, until the moment is reached when they need to be replaced. This means that they are ‘sacrificial anodes’.
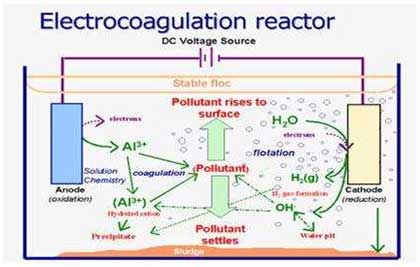
An electrochemical reactor consists of a tank with two submerged electrodes connected to a power source. When a certain voltage is reached between the electrodes, reduction processes on the cathode and oxidation processes on the anode begin (generating the ion Al3+ if the anode is aluminum and Fe3 if it is steel). A series of processes then takes place: ionization, destabilization, oxidoreduction, electrolysis, free radical formation, electromagnetic field formation, and emulsion breaking and separation.
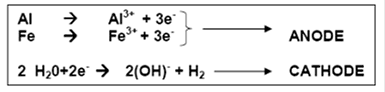
In the vicinity of the anode, the generation of oxygen resulting from the oxidation of the water causes the formation of H+ ions which, due to their charge, are attracted to the cathode. On the cathode, the reduction of water to form hydrogen causes the formation of hydroxyl (OH-) ions which, unlike the H+ ions, are attracted to the anode. The increase in pH generated on the cathode can encourage the precipitation of the metallic ions contained in the wastewater.
Different Elco Reactors
Elco Pro Series Models (Reactor with one anode and cathode, and with dozens of sacrificial blades)In this configuration, ELCO PRO SERIES, reactor is made up of one anode and one cathode and, dozens of sacrificial metal blades (steel). The reaction cell contains a series of metal blades placed parallel to each other. The influent to be treated is introduced into the bottom of the chamber and dispersing it evenly as it moves upward through the electrodes. Direct Current (Vdc) is introduced into the cell by attaching the positive (+) and negative (-) leads to the first and last terminal, located outside the chamber. The liquid then becomes a conductor, allowing the DC current to pass freely throughout the chamber. The electrodes react to the current by releasing charged metal ions into the influent at a rate of 0.04 kg / m3 treated. The flooding of electrons into the influent neutralizes charged particles, causing them to be pulled out of suspension. Electrocoagulation through the reaction cell produces several distinct electrochemical results independently.
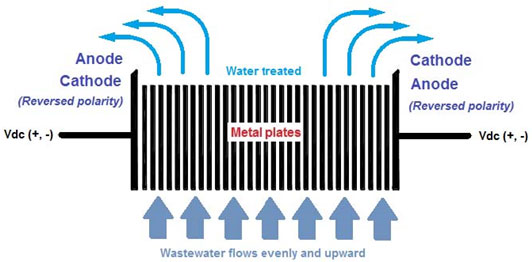
The parallel arrangement of plates is electrically similar to a single cell with many electrodes and interconnections. The electric current is divided between all the electrodes in relation to the resistance of the individual cells. ELCO PRO SERIES have the advantage versus ELCO (plus series) because less electricity is required. In this instance the sacrificial electrodes are placed between the two parallel electrodes without a middle electrical connection.
When an electric current is passed through the two electrodes, the neutral sides of the conductive plates will be transformed to charged sides, which have opposite charge compared to the parallel side beside it. Thus, during the process, the positive side undergoes anode reactions, while on the negative side, cathode reaction is encountered. The released ions neutralize the charges of the particles and thereby initiate coagulation. In addition, as water containing colloidal particulates, oils, or other contaminants move through the applied electric field, there may be ionization, electrolysis, hydrolysis, and free-radical formation which may alter the physical and chemical properties of water and contaminants. As a result, the reactive and excited state causes contaminants to be released from water and destroyed or made less soluble. The diagram below illustrates the structure of the main system, in this case, composed of four electrolytic chambers with dozens of sacrificial blades.
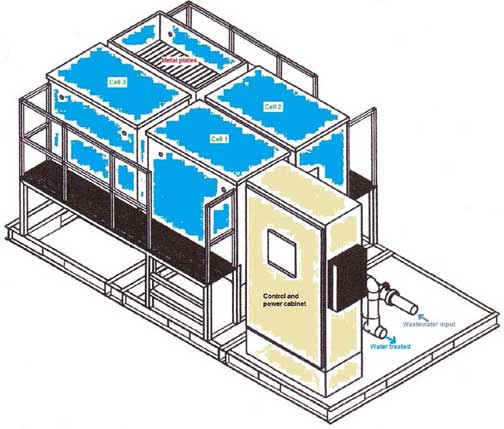
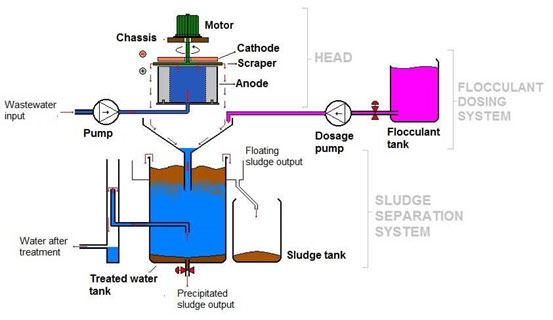
The main operational problem of some other electrocoagulation systems arises from the decommissioning of the anode as a result of the formation of a coating formed by the products of the reaction. The insoluble hydroxides can gather on the surface of the anode, thus impeding the electrocoagulation process. In order to prevent this problem from occurring, this reactor is designed in such a way that the water being treated flows past the anode and cathode, thus enabling the electrocoagulation process and, at the same time, automatically cleaning the anode to considerably reduce maintenance needs.
This system consists of various different parts: the head, the sludge separation system, and the flocculant dosing system. The head consists of the anode – which rests on the frame of the system -and the cathode, which is attached to a mobile structure with a pneumatic piston that allows the anode to be repositioned rapidly. A 1 mm thick scraper is situated between the anode and the cathode. The scraper is attached to the motor axle and is for removing the sludge that adheres to the electrodes and ensuring uniform wear on the anode.
The anode is toroidal in shape and has a cylindrical concentric cavity inside. The water being treated is driven by a pump towards the lower part of the anode. As a result of the action of the inlet pump, the internal cavity of the anode fills with water until the water overflows at the top, passing through the 1 mm gap between the anode and the cathode. This is where the water electrolysis process takes place.
The water that overflows between the anode and cathode is collected in the lower part of the system using a conical funnel (depending on the model). It is at this point that – depending on the system model – the flocculant is added using a dosing system that consists of a storage tank and a peristaltic pump regulated by the programmable controller.
Lastly, the treated water flows towards the sludge separation system where it is stored in the treated water tank and the floating sludge, precipitated sludge, and clarified water are separated. The floating sludge is sent to be decanted into a second tank to be extracted later on. The precipitated sludge is discharged via a manual valve installed on the treated water tank. The treated water is extracted using a simple separation system.
Automation and Control
ELCO is a totally automatic system that allows for continuous and controlled electrocoagulation.
The system consists of the following elements
Control cabinet for monitoring and regulating the process with the following features- Programmable controller
- AC/DC converter
- Touch screen
- Various electrical elements
- Inlet pump for water to be treated
- Outlet pump for clean water
- Agitation motor (in the case of the plus configuration)
- Inlet and outlet electrovalves
- Scraper motor (in the case of plus configuration)
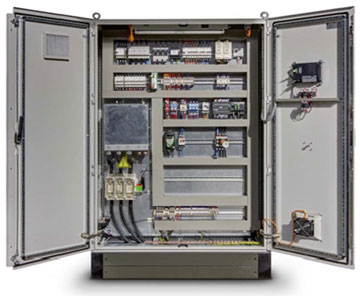
Our ELCO system incorporates a touch screen for regulating and monitoring the process. The figure below illustrates this screen. The operator uses these displays to activate and deactivate the process, view the status of all elements, set the amperage to the required level, call up the energy consumption of the system, adjust the anode, and reset the acoustic alarm.
Elco System
ELCO is a powerful technology able to remove TSS, oil suspension and big part of the organic contamination. We can achieve 90-95% removal of COD and more than 98% removal of oil content. In other cases, we complement the technology according to the effluent limits of the Clients.
ELCO executes a controlled electro-chemical process that destroys toxic compounds. In almost all cases, ELCO improves the chemical-physical traditional treatment, so that in addition to flocculate and coagulate, ELCO is also executing a partial oxidation of the contamination biodegradable and a partial oxidation of the contamination not biodegradable. In fact, depending on how we proceed and depending on the quality of the water to treat, we can oxidize soluble COD in yields up to 95%. ELCO (plus configuration) cleans automatically the electrodes. Our two configurations (plus or sacrificial blades) work in a continuous way and, control and reduce the amount of power consumed; all these features show you the difference it has over many other technologies.
The following effects occur during the process
- Removal of heavy metals
- Removal and separation of oils and fats
- Oxidation of organic material/breaking of organic molecules
- Reduction and/or elimination of ecotoxicity
- Removal of bacteria, viruses, and parasites
- Removal and separation of suspended solids and colloids
- Elimination of smells
- System with or without a sludge separation system.
- System with or without a flocculant dosing system.
- System with or without pH and conductivity control functions.
- Depending on the volume of water to be treated, a fewer or greater number of heads can be installed without varying the rest of the system.
- The use of different alloys and materials for anodes depending on the type of water to be treated ensures that the optimum anode for each process is used.
- In the case of the plus configuration, the vertical positioning of the anode and cathode facilitates the flow and the automatic cleaning of both elements. The system is low-maintenance.
- In the case of the plus configuration, the automatic regulation of the distance between the anode and the cathode makes it possible to treat different volumes and yields.
- Automatic regulation of power and voltage depending on the conductivity ensures a constant yield.
- In the case of the plus configuration, the generation of microbubbles by the agitator in the reception tank for the treated water enables the automatic flotation and separation of sludge
- In the case of Elco Pro Series configuration, we assure less electricity and time needed to treat higher flow rates.
Elco Plus Models (includes a sludge separation system)
Model | Max Volume (m3/h) | Max Volume (GPM) | Installed Power |
ELCO PLUS 1/5 | 1 m3/h | 5 GPM | 10 KW |
ELCO PLUS 2/10 | 2 m3/h | 10 GPM | 20 KW |
ELCO PLUS 4/20 | 4 m3/h | 20 GPM | 40 KW |
Elco Pro Models (sacrificial blades)
Model | Max Volume (m3/h) | Max Volume (GPM) | Installed Cells |
ELCO PRO 30/130 | 30 m3/h | 130 GPM | 1 |
ELCO PRO 60/260 | 60 m3/h | 260 GPM | 2 |
ELCO PRO 120/520 | 120 m3/h | 520 GPM | 4 |
ELCO PRO 180/780 | 180 m3/h | 780 GPM | 6 |
In the case of flows higher than 4 m³/h, as many reactors as are required to treat the desired volume can be installed. In each case, the most suitable system for the required process can be used.
Examples of the elimination of contaminants
ORGANIC MATTERThe reduction in DQO and DBO5 matter is brought about by the different effects of the process:
- Flocculation of organic matter
- Oxidation of organic matter
- Breaking of large molecules
- Indirect oxidation as a result of the generation of strong chemical oxidants
The electrochemical reduction process results in the breaking up and separation of the oils and fats present in the water, regardless of whether or not they are already emulsified. These oils and fats are separated by means of flotation through the generation of microbubbles.
HEAVY METALSHeavy metals are removed by an oxidoreduction process that produces insoluble metallic hydroxides that become trapped in the sludge.
SUSPENDED SOLIDS AND COLLOIDSThe electrochemical process results in a stable state of solid particles that are less colloidal or emulsified (or soluble) than at the state of equilibrium. When this occurs, the contaminants form hydrophobic components in the form of larger flocs that can be removed easily by means of flotation or decantation as required.
ECOTOXICITYThe removal of toxic organic components and/or heavy metals eliminates the ecotoxicity of the water, allowing it to be disposed of or reused. In some cases, this method can be used as a preparatory step prior to biological treatment.
ELIMINATION OF WATER HARDNESSThe removal of calcium and magnesium cations and salts such as sulphate, carbonate, and phosphate salts by means of electrochemical precipitation enables a reduction in the hardness of the treated water and prevents the formation of incrustations and biofilms in pipes and installations. This is extremely useful as a preparatory step prior to inverse osmosis processes (to lengthen the life of membranes) and for maintaining refrigeration water systems (since it prevents colonization and contamination by legionella bacteria).
REMOVAL AND DISINFECTION OF BACTERIA, VIRUSES, AND PARASITESThe electric discharge, temperature, and generation of oxidants produce a highly germicidal effect that can ensure that all effluent treated by means of electrocoagulation is complete free from pathogens.
This benefit of electrocoagulation is of interest in the following fields:- Legionella disinfection
- Purine hygienization
- Making wastewater or drinking water drinkable
The table below shows the percentage rates for the elimination of contaminants by ELCO.
Contaminant | ‘Pure’ concentration | Following electrocoagulation | Elimination rate |
Aldrin (pesticide) | 0.063 mg/l | 0.001 mg/l | 0.984 |
Aluminum | 224.00 mg/l | 0.69 mg/l | 0.9969 |
Americium-241 | 71.99 pCi/L | 0.57 pCi/L | 0.992 |
Arsenic | 0.30 mg/l | Less than 0.01 mg/l | 0.967 |
Bacteria | 110,000,000 cfu | 2.700 cfu | 0.9999 |
Total coliform bacteria | More than 2,419.2 mpn | 0.0 mpn | 0.9999 |
Barium | 0.0145 mg/l | Less than 0.0010 mg/l | 0.931 |
Boron | 4.86 mg/l | 1.41 mg/l | 0.7098 |
Cadmium | 0.1252 mg/l | Less than 0.0040 mg/l | 0.9681 |
Calcium | 1,321.00 mg/l | 21.40 mg/l | 0.984 |
Cipermetrin (pesticide) | 1.30 mg/l | 0.07 mg/l | 0.946 |
Chlorieviphos (pesticide) | 5.87 mg/l | 0.03 mg/l | 0.995 |
Cobalt | 0.1238 mg/l | 0.0214 mg/l | 0.8271 |
Copper | 0.7984 mg/l | Less than 0.0020 mg/l | 0.9975 |
Chromium | 139.00 mg/l | Less than 0.10 mg/l | 0.9992 |
DDT (pesticide) | 0.261 mg/l | 0.002 mg/l | 0.992 |
Diacin (pesticide) | 34.00 mg/l | 0.21 mg/l | 0.994 |
E coli bacteria | More than 2,419.2 mpn | 0.0 mpn | 0.9999 |
Enterococcus bacteria | 83 mpn | Less than 10 mpn | 0.8287 |
Tin | 0.213 mg/l | Less than 0.0200 mg/l | 0.9061 |
Fluoride | 1.1 mg/l | 0.415 mg/l | 0.6227 |
Phosphate | 28 mg/l | 0.2 mg/l | 0.9928 |
Iron | 68.34 mg/l | 0.1939 mg/l | 0.9972 |
Lindane (pesticide) | 0.143 mg/l | 0.001 mg/l | 0.993 |
Magnesium | 13.15 mg/l | 0.0444 mg/l | 0.9966 |
Manganese | 1.061 mg/l | 0.0184 mg/l | 0.9827 |
Mercury | 1.15 mg/l | Less than 0.03 mg/l | 0.9739 |
Molybdenum | 0.18 mg/l | 0.04 mg/l | 0.806 |
Nickel | 183 mg/l | 0.07 mg/l | 0.9996 |
Nitrate | 11.7 mg/l | 2.6 mg/l | 0.7778 |
Nitrite | 21 mg/l | 12 mg/l | 0.4286 |
Nitrogen (TKN) | 1,118.8 mg/l | 59.08 mg/l | 0.9472 |
Petroleum hydrocarbon | 72.5 mg/l | Less than 0.2 mg/l | 0.9972 |
Lead | 0.3497 mg/l | Less than 0.0250 mg/l | 0.9285 |
Plutonium-239 | 29.85 pCi/L | 0.29 pCi/L | 0.99 |
Potassium | 200 mg/l | 110 mg/l | 0.45 |
Propetamphos (pesticide) | 80.87 mg/l | 0.36 mg/l | 0.996 |
Radium | 1093.0 pCi/L | 0.1 pCi/L | 0.9999 |
Selenium | 68 mg/l | 38 mg/l | 0.44 |
Silicon | 21.07 mg/l | 0.10 mg/l | 0.995 |
Sodium | 8,690 mg/l | 5,770 mg/l | 0.336 |
Sulphate | 104 mg/l | 68 mg/l | 0.3461 |
Uranium | 10.8 mg/l | 0.1 mg/l | 0.9907 |
Vanadium | 0.2621 mg/l | Less than 0.0020 mg/l | 0.9924 |
Zinc | 221.00 mg/l | 0.14 mg/l | 0.999 |
Electrocoagulation Applications
- METALLURGY INDUSTRY
- Oxidation and precipitation of heavy metals
- REFRIGERATION TOWERS
- Prevention of incrustations and elimination of legionella
- FOOD INDUSTRY
- Disinfection and reuse of water
- Treatment of alpechines in oil production
- Treatment and elimination of fats in waste
- Elimination of high organic and solid load rates
- Treatment of effluent containing blood
- LIVESTOCK FARMING
- Treatment of purines (reduction in DQO, nitrogen and phosphorus, and hygienization)
- MINING INDUSTRY
- Elimination of metals, salts and suspended solids
- PHARMACEUTICAL INDUSTRY
- Elimination of ecotoxicity in waste
- Destruction and elimination of organic molecules and DQO/DBO5
- DECONTAMINATION OF UNDERGROUND WATER
- Removal of metals, hydrocarbons, pesticides and phytosanitary substances, etc.
- TREATMENT OF SEEPAGE
- Reduction and elimination of heavy metals, organic matter, nitrogen compounds, salts, and other contaminants to yield a quality good enough to enable the reutilization of the seepage water for irrigation and cleaning or disposal of the water.
- COSMETICS INDUSTRY
- Reduction in organic load, elimination of colors and fats
- PAPER INDUSTRY
- Removal of fibres, solids, and organic load
- TEXTILE INDUSTRY
- Removal of color and organic load
- CHEMICALS INDUSTRY
- Removal of metals, salts, organic matter, smells and colors, reduction in ecotoxicity, and so on
- METAL PLATING INDUSTRY
- Removal of heavy metals
- PETROLEUM INDUSTRY
- Removal of hydrocarbons, metals, etc.
Advantages of Elco Electrocoagulation
- Treatment for multiple contaminants
- Low sludge formation
- Low installation and assembly costs
- Low operating costs
- Does not require chemical products
- Elimination of colours and odours
- Instant treatment
- Possibility of modular system/enlargement
- Does not require building work
- Automatic operation, low maintenance
- Does not require a large amount of space, possibility of carrying out treatment within the production process
Comparative analysis with other systems
- Treatment for multiple contaminants.
- Requires much less space and building work.
- Generates 90% less sludge in comparison with traditional physicochemical processes, easy filtration.
- The conductivity and salts are favorable to the decontamination process without increasing the effect, reducing in the obtained treated water.
- The process tends to bring the treated water close to a neutral pH.
- Precipitates heavy metals such as chromium 6 that require a different type of treatment to other metals.
- Cleans and disinfects the end product of pathogens.
- Generates inert, hygienic sludge that can be used as compost.
- Eliminates incrustations and legionella.
- Has operating costs of around 50 – 60% less than traditional physicochemical processes.